Fleet strategies to maximize your cost savings potential
August 25, 2021
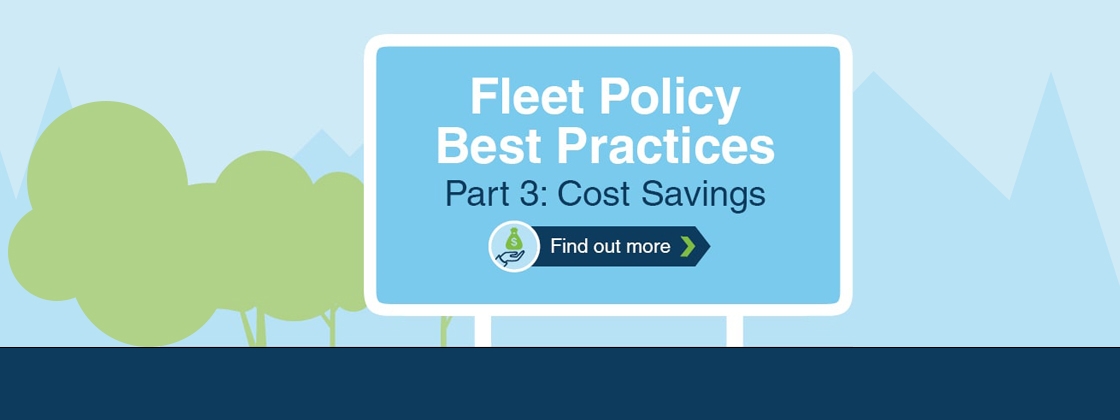
Did you know that fleet costs are a top five controllable expense?
Depending on the industry, fleet can account for nearly 20% of total corporate operating costs. What actions are you taking today to reduce your company’s fleet expenses?
In 2020, Element’s strategic consulting team identified over $1.5 billion in cost savings for clients. Keep reading to discover best practices to reduce costs in the areas of vehicle depreciation, fuel, and maintenance. These three areas make up on average 77% of total fleet costs for companies in North America.
Depreciation
Best practices to reduce depreciation expense
- Sync acquisition and disposition timing by establishing a regular replacement rhythm. Where feasible, place vehicle orders in the fall when the new model year is released to avoid further vehicle depreciation.
- Are you planning to offer a vehicle purchase program for your employees? Establish a resale policy which benefits both parties. By selling vehicles close to fair market value, the company can reduce depreciation costs and the driver can benefit from a reasonable sale price, while avoiding dealer markup and transaction fees.
- If a single OEM (Original Equipment Manufacturer) can meet your vehicle needs and volume requirements, we recommend sourcing from one partner to improve tier discounts through economies of scale.
Client success story
A client who historically ordered from a mix of OEMs for similar vehicle types was looking for ways to reduce spend.
Element’s strategic consulting team created a life cycle cost analysis to compare vehicle total cost of ownership. The analysis demonstrated the benefits of a leveraging a single OEM for a greater incentive discount.
The result was $1.4MM in estimated life cycle savings Savings came from increased tier incentives (approximately $300 per unit) and shifting a portion of the fleet from SUVs into sedans.
Fuel
Best practices to reduce fuel expense
- Establish a driver policy for fuel purchases to make employees aware of which fuel type is most appropriate for their vehicle. Opting for regular fuel rather than premium for instance can help you save costs.
- Determine and communicate reasonable driver limits for car washes.
- Here’s an example fleet policy: “A driver may purchase up to two car washes per month up to $20, utilizing pay at the pump when purchasing fuel. Car washes deemed excessive by the fleet office will be the driver’s financial responsibility.”
- Leverage exception reporting to detect fuel fraud. Element’s fuel program allows for extra controls over fuel spend such as limiting the number of transactions within 24 hours or by vehicle type.
Client success story
A client was concerned with fueling activity as both frequency and dollar volume limits were exceeded.
Over 600 transactions were reviewed, detailing time stamps, costs, product types and other relevant data points.
The analysis uncovered that several fuel cards had likely been stolen and were being used fraudulently. A detailed summary of transactions and analysis were delivered to the client.
Cards with fraudulent activity were cancelled and reissued appropriately.
Fraudulent activity ceased, saving over $600 per day per card*
*Based on days with high fraud volume per card
Maintenance
Best practices to reduce maintenance expense
- Network utilization: establish a policy and educate drivers on the importance of leveraging a managed network maintenance location. Take advantage of the negotiated pricing and buying power to reduce transaction costs.
- Select the appropriate case limits for maintenance transactions to reduce approval time and subsequent driver downtime.
- Monitor and manage preventative maintenance compliance. Through Element’s maintenance program, proactive preventative maintenance notification reminders are sent to drivers based on OEM guidelines. Adhering to routine preventative maintenance can help prevent costly repairs and associated vehicle downtime.
Client success story
A client in the retail industry had a case limit of only $500, while 64% of expense occurred in $500 to $1,000 range.
39% of tire expense and 64% of preventative maintenance (PM) transactions were completed at dealer and independent shops.
Element’s strategic consulting team performed a maintenance deep dive on tires, PMs, roadside/towing, brakes, and transmissions.
They quantified the potential savings of steering additional volume to key national accounts and recommended increasing the case limit to $1,000 to reduce approval time and downtime.
This led to a 5,388 reduction in downtime hours and $540K in downtime savings.
The client also realized $185K in annual savings by shifting volume from dealers and independents to select national providers.
Download the full infographic
DownloadLooking for more fleet insights? Check out part one and two of our series, focused on fleet safety and sustainability.
Never miss an update
Subscribe for more news and thought leadership from Element.