Your comprehensive guide to fleet maintenance costs
February 22, 2024
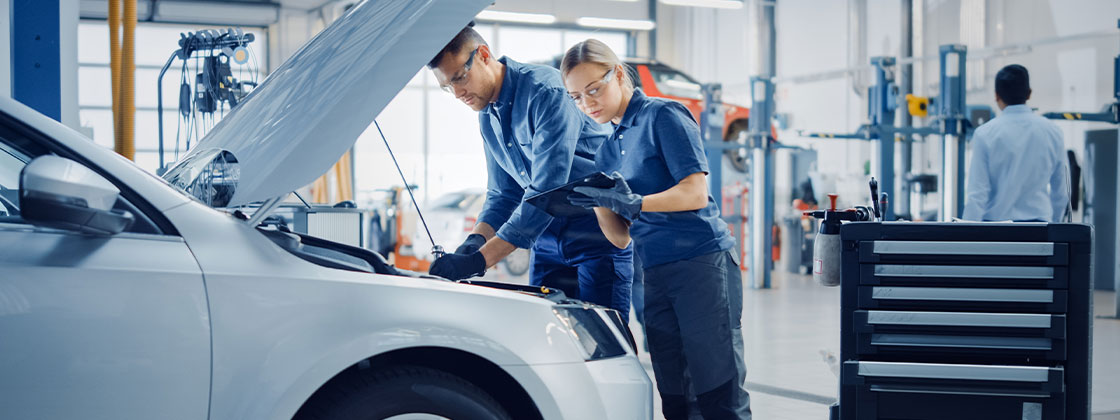
Fleet maintenance and repair costs have risen significantly, going from single digit increases to double digit increases over the last few years. Whether you manage your fleet on a local or global scale, there are many things you can do to lower fleet maintenance costs and influence your fleet’s total cost of ownership (TCO). You can also prevent fleet productivity loss by taking actions to reduce vehicle downtime.
Reduce vehicle downtime
DownloadWhy is fleet vehicle maintenance important?
Maintaining fleet vehicles is one of the top three fleet expenses for businesses, but it also offers a significant opportunity for cost reduction. This involves proactive and regular maintenance, repairs, and upkeep for a fleet. It includes preventive measures like oil changes, tire rotations, and promptly addressing replacements and repairs. The goal is to keep your fleet in optimal condition, ensuring smooth operations and safeguarding vehicle lifespan.
Fleet maintenance trends and outlook for 2024
In recent years, fleet maintenance costs have consistently increased due to factors like parts shortages, rental delays, labor scarcity, and rising raw material expenses. Understanding these causes is crucial for managing effective cost strategies.
- Parts shortages and delays: Inflation and supply chain challenges have significantly impacted fleet vehicle maintenance. Repair shops are urged to leverage used parts for faster repairs. Rising prices of replacement parts, tires, and glass have increased repair costs. Tire costs rose by 8.5% over the past year. Parts delays will remain a challenge in North America in 2024, with body shops taking longer to acquire parts compared to 2019.
- Complexity of repairs: In recent years, vehicle repairs have become more complex, leading to longer maintenance times at repair shops. Additionally, the integration of advanced technology and safety systems in windshields has resulted in higher costs for replacement claims. These trends highlight the need for specialized technician expertise in automotive maintenance.
- Rental cost and vehicle availability: Clients face high rental costs due to increased downtime caused by parts shortages and limited availability of new vehicles. Some regions are experiencing a rental vehicle shortage due to high demand and longer rental use.
- Labor shortages: The scarcity of qualified service technicians has resulted in higher labor rates and extended repair times. Shops pay more for available technicians due to recruitment and retention challenges. The industry needs to add 46,000 more technicians by 2026 in the United States and expects 54,000 new job openings for technicians by 2031 in Canada.
- Raw material costs: Supply chain issues are impacting many segments of the economy including the cost of raw materials. Notably, crude oil, rubber, and lubricant costs have increased, with lubricant prices following the crude oil market.
- Synthetic oils: The widespread adoption of synthetic oils by original equipment manufacturers (OEMs) is increasing in fleet vehicles. While this raises the cost per oil change, it leads to fewer shop visits. Inflationary pressures have driven up oil change costs by over 9% between 2022 and 2023, and this trend is projected to continue.
5 strategies to reduce fleet maintenance costs
- Strengthen preventive maintenance: To minimize unexpected repairs, prioritize regular preventive maintenance. Keep up with schedules to reduce downtime and safeguard the lifespan of your vehicles. While using long-lasting synthetic oil when recommended by OEMs can lengthen the intervals between oil changes, don't overlook tire rotations and critical vehicle inspections (e.g., brakes) for improved safety and productivity. Use automated driver alerts and exception reporting to stay on top of preventive maintenance and identify vehicles due for service.
- Leverage status tracking: Managing vehicle downtime is critical to fleet productivity. Clients have found value in repair status tracking, especially given parts shortages, and rising rental expenses. Element fleet management offers managed rental services, providing consistent follow-up with repair shops to track repair estimated time of arrival (ETA) and minimize extended rental time and costs.
- Capitalize on fleet discounts: Joining a structured maintenance program comes with perks, such as access to a nationwide maintenance network with negotiated pricing. Element's national account maintenance network offers cost savings of 8% - 15%. Drivers can choose from our extensive North American fleet maintenance and repair network, which includes 50,000 national and independent providers.
- Opt for higher quality parts: Avoid using medium to low-quality parts as they may result in higher costs in the long run. Prioritize higher quality parts to maximize fleet vehicle performance and reduce breakdowns, ensuring efficient operations.
- Invest in driver training: Driver behavior plays a crucial role in managing maintenance costs. Evaluate factors like speeding, excessive idling, harsh braking, and hard cornering among your drivers. Encourage efficient driving practices to prevent accidents and unnecessary repairs. Keep safety policies and driver safety training up to date. Element can collaborate with you to identify opportunities for reducing maintenance costs and risks.
Unique maintenance factors for electric vehicles
Based on a recent Element maintenance analysis, electric vehicles (EVs) typically require 40% less maintenance spend overall compared to Internal Combustion Engine (ICE) vehicles. With fewer moving parts, they require less frequent maintenance visits. However, there is added complexity and cost considerations involved in glass/windshield maintenance and collision repairs. This highlights the changing landscape of automotive maintenance. This emphasizes the need for specialized expertise in servicing EVs.
Glass and windshield maintenance
Auto glass services for EVs come with a premium price tag, particularly due to the advanced technology embedded in the windshield. The cost of replacement windshields for EVs far exceeds that of ICE vehicles, with additional expenses for Advanced driver assistance systems (ADAS) calibration, making repairs and replacements more intricate and costly.
Collision repair costs and cycle time
Data from a comprehensive maintenance study comparing EVs and ICE vehicles revealed that EVs incurred significantly higher repair costs, labor hours, and part replacements. This is attributed to the construction methods, materials, and industry capacity constraints specific to EV servicing. The repair cycle time for EVs was notably longer due to the specialized procedures required.
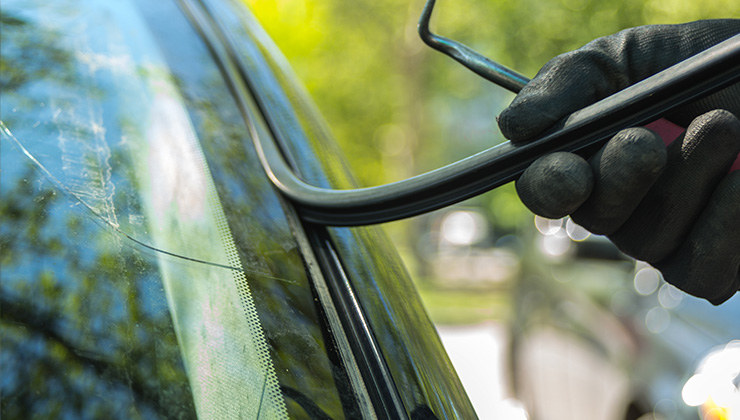
Element maintenance study comparing ICE and EV repairs
A controlled client maintenance study from 2022 to 2023 compared a Tesla Model 3 and Chevrolet Equinox. The results showed higher maintenance repair costs, labor hours, parts replaced, and cycle time for the EV when compared to the ICE vehicle. Despite the lower maintenance costs overall for EV versus ICE vehicles, added complexity contributes to higher transactional repair costs.
- 65% higher repair costs – driven by cost and quantity of parts and labor
- 29% higher labor hours – due to more labor-intensive operations for scanning and calibration
- 95% more parts replaced – with stringent OEM guidelines and less repairable materials
- 47% more cycle time – driven by more parts, backorders, and capacity constraints within shops
Please note this is a client specific example. Results may vary given environmental factors and vehicle utilization.
Key impacts on maintenance costs for EVs
The maintenance and repair of EVs are influenced by several key factors, including:
- Repair Industry Capacity: The slow adoption and limited capacity of repair shops to handle EVs result in considerable investments in equipment and longer lead times for servicing.
- Parts Cost and Availability: EVs utilize advanced lightweight materials, leading to higher component costs and longer lead times for parts supply, creating disparities with legacy ICE vehicle supply chains.
- Labor Cost: Limited repairability of materials such as aluminum, as well as the need for specialized operations like high-voltage system calibration, contribute to higher labor rates and extended downtime for EV repairs.
- Downtime: Delays in parts sourcing and specialized repair operations result in longer downtime for EVs compared to ICE vehicles, impacting overall repair cycle time.
How to minimize fleet vehicle downtime
Vehicle downtime can be a formidable expense for fleet management, with fleets losing an average of $448 to $760 per day per vehicle. To boost time in-service and profit, fleet managers can emphasize preventive maintenance, deploy telematics for in-depth maintenance insights, and provide driver training to reduce the incidence of collisions and consequently, repair costs. Discover more about reducing fleet vehicle downtime.
Make an impact on your fleet costs today
Ready to make an impact on your fleet’s TCO by reducing your maintenance expenses? Find out more about Element’s fleet maintenance and repair services or get in touch with us!
Never miss an update
Subscribe for more news and thought leadership from Element.